Автоматизированная система управления предприятием в чулочно-носочной промышленности
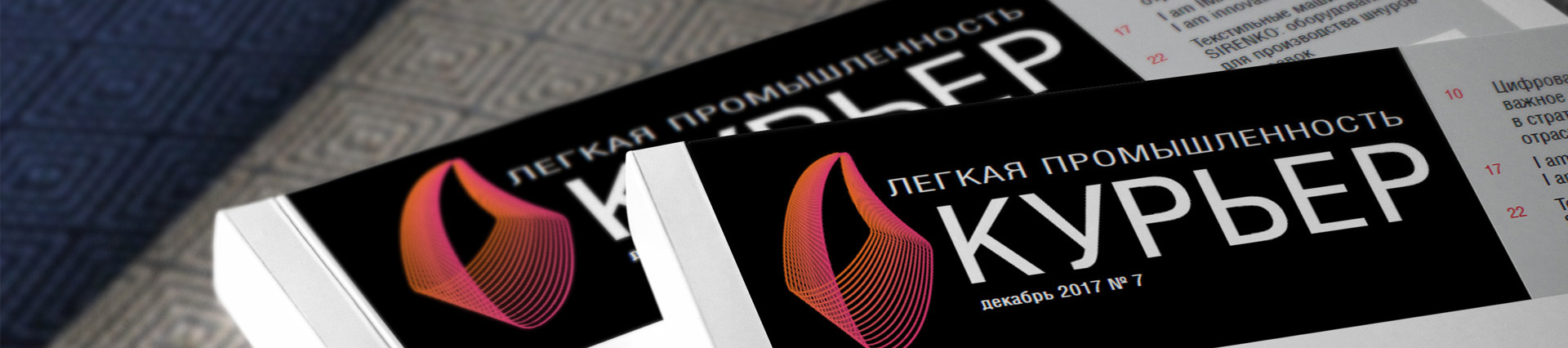
В 2012 году Российская Федерация вступила во Всемирную торговую организацию (ВТО). Наша промышленность лишается преимуществ на внутреннем рынке: снижаются ввозные пошлины на готовые виды продукции, рынок становится более прозрачным и конкурентным. Наиболее чувствительно последствия вступления в ВТО скажутся на легкой промышленности. Все ли предприятия готовы к таким изменениям и как сделать предприятие более эффективным, гибким, прозрачным и привлекательным для инвесторов и, одновременно, повысить рыночную стоимость действующих производств?
Автоматическая линия формировки и упаковки чулочно-носочных изделий
Посмотрим на официальные цифры. В период с 2005 по 2008 гг. производство чулочно-носочных изделий выросло с 367,9 до 441,7 пар (примерно на 20%). За этот же период импорт вырос более чем в два раза — с 477,9 до 1125 млн пар (примерно на 136%). Эти цифры обусловлены тем, что объем потребления в этот период вырос в 2 раза. Рост продаж осуществлялся, в первую очередь, за счет увеличения реализации импортного товара. Растущие доходы мотивировали население тратить больше денежных средств на одежду. Кризисный 2009 год поменял статистику продаж в чулочно-носочной промышленности, но с 2010 года все опять возвращается к прежним показателям.
Представленные данные говорят о том, что рынок насыщен и предложение опережает спрос. Объем импорта значительно превышает внутреннее производство, и его доля в общем объеме продаж снижается крайне медленно. Если посмотреть на состояние отрасли — его лидерами являются предприятия, созданные при Советском Союзе, с устаревшей инфраструктурой и коммуникациями. К основным конкурентным преимуществам подобных предприятий надо причислить их многолетнюю историю, наличие сформировавшегося коллектива специалистов, подготовленных сотрудников. Но есть и минусы: устаревшая схема производственного процесса, разные группы оборудования, выпущенные различными производителями и имеющие разные производственные и сервисные подходы.
Самым крупным предприятием на российском рынке является ЗАО «Смоленская чулочная фабрика» (год запуска 1952). Годовой объем выпуска изделий за 2010 г. составил 55161 тыс. пар.
Вторым в рейтинге идет ОАО «ГАММА», основанная в 1934 году. Количество выпущенной продукции за 2010 г. — 42843 тысячи пар.
Замыкает тройку лидеров ООО «Текстильное трикотажное объединение «Клинволокно» с годовым объемом выпуска в размере 33191 тысяч пар по данным за 2010 год. Фабрика была открыта в 1929 году, изначально как предприятие по производству химических волокон.
Все предприятия вошли на рынок с большим штатом, непрофильными активами, устаревшими парком оборудования и технологическим процессом. Самая сложная задача — перейти от плановой экономики с системой распределения к рыночным отношениям и начать конкурировать за реального потребителя с поставщиками импортной продукции. На первый план вышел покупатель, который рублем голосует за продукцию.
Для эффективной борьбы за потребителя необходимо выстроить систему гибкого производства, при которой разработка новых изделий и ввод их в ассортимент становится постоянной. Можно привести в пример итальянскую компанию Сalzedonia. Очень современное производство с годовым объемом выпуска готовых изделий, сопоставимым со Смоленской чулочно-носочной фабрикой, а именно, более 36 млн изделий в год. Отдел перспективных изделий итальянской компании делает за сезон (6 месяцев) около 600 образцов изделий, из которых 100 принимаются в производственную программу. Можем сопоставить численность сотрудников обоих предприятий.
Как стремиться к аналогичным показателям в условиях российской действительности?
Для начала необходимо сказать несколько слов об организации производственной схемы на чулочно-носочном предприятии. Нижеприведенная информация соответствует современным тенденциям и предполагает использование оборудования, которое можно будет подключить к системе автоматизированного управления предприятием.
Схематически производственную цепочку можно разделить на следующие блоки:
В идеальном варианте сама фабрика должна быть построена по данному линейному принципу, что намного упрощает систему транспортировки полуфабриката в рамках предприятия. К сожалению, лишь единицы российских предприятий могут похвастаться подобной структурой (среди них «Акос Текс»), большинство же располагается на нескольких этажах, что значительно усложняет внутренние логистику и учет, а также значительно затрудняет автоматизацию производства в целом.
После полной компьютеризации кругловязальных автоматов к основным достижениям в усовершенствовании данного оборудования необходимо причислить узел автоматической кеттлевки мыска, когда вязальный автомат вяжет носок, после чего сам же его и зашивает. На сегодняшний день подобными агрегатами могут быть оснащены большинство кругловязальных автоматов итальянского производства. Так, при заказе парка оборудования узел автоматический зашивки мыска предлагают своим клиентам такие производители, как Lonati, Busi, Santoni и прочие. При формировании парка вязального оборудования каждый клиент сам определяет комплектацию, ведь при установке механизма автоматической зашивки стоимость автомата возрастает в среднем на 25%, а производительность несколько снижается (на время простоя при переносе отвязанного изделия на узел зашивки). Зона обслуживания отдельно стоящих кеттельных машин типа «Россо» или «Конти» составляет порядка 15–20 вязальных автоматов. Таким образом, изначальные инвестиции существенно возрастают. Тем не менее, вязальные автоматы с узлом автоматического зашива мыска более универсальны, при их использовании удается объединить вязальный и швейный цеха — тем самым можно не только улучшить и ускорить производственный цикл в целом, но и сократить затраты на лишний обслуживающий персонал и дополнительное оборудование (например, для автоматической выворотки изделий). Также не следует забывать, что универсальный автомат позволяет сократить производственные площади. Нам видится, что будущее все-таки за подобными многофункциональными автоматами.
В России традиционно выпускной цех также разделяют на два отдельных участка, соответственно: формировка чулочно-носочных изделий, после чего его упаковка. Причем, если рассмотреть количество работников, занятых на данном этапе, то на них приходится чуть ли не 50% от всего производственного штата. Как результат — один из самых низких КПД во всей производственной цепочке. Причем, традиционно данные цеха имеют 8-часовую 5-дневную рабочую неделю, что ведет к дальнейшему раздуванию штата. Одним словом, данный участок на большинстве российских предприятий является наиболее устаревшим и наименее рентабельным.
За последние несколько десятков лет совершен настоящий прорыв в автоматизации операций выпускного цеха. Главным новатором в данной отрасли выступила итальянская компания Autotex. Основным направлением их деятельности является разработка и изготовление упаковочного и формировочного оборудования. Упаковочные линии — это многофункциональные автоматы, осуществляющие одновременно несколько операций. Например, автоматическую подачу этикетки, ее печать, пришив этикетки, нанесение клейкого стикера, вставки вешалки и другое. То есть, оператор помещает на загрузочную ленту сложенную пару или несколько пар носков, после чего на выходном конвейере можно получить упакованное в пакет изделие, готовое к отгрузке конечному клиенту. Причем, производительность данного автомата чрезвычайно высока — в среднем 800 пар в час. Таким образом, один оператор даже при 8-часовой рабочей смене выпускает в среднем 6400 готовых изделий, а при двух сменах с одного автомата можно получить 12800 пар. И это при двух операторах.
Пример этикетки отпечатанной Autotex
Отдельного упоминания заслуживают формировочные автоматы производства фирмы Autotex. Модель Т32 оснащена рядом узлов, позволяющих добиться не только высококачественной формировки, но и максимальной автоматизации и оптимизации производства. Если рассматривать качественную составляющую, то необходимо упомянуть такие узлы как: устройство предварительного разогрева форм (изделие помещается на горячую форму, при обработке паром из-за отсутствия разницы температур внутри и снаружи носка пар не конденсируется, а проникает непосредственно в структуру пряжи, обеспечивая максимально качественную фиксацию изделия; кроме того, снижается потребление пара и электроэнергии); эргономичная паровая камера на две формы (чем дольше изделие обрабатывается паром, тем лучше конечный результат); электрический пресс, два туннеля сушки — горячим и холодным воздухом (охлаждение отформированных изделий позволяет убрать из производственной цепочки участок «отлежки», когда необходимо дождаться окончательного высыхания и усадки изделия до осуществления его упаковки); наконец, принципиально новое устройство съема, чрезвычайно бережно обращающееся с изделием, чтобы избежать возможных заломов. Автомат оснащен 31 формой, съем идет по одному носку. Это было сделано для того, чтобы была возможность подключения формировочного автомата к упаковочной линии.
Такие линии установлены на итальянском предприятии Calzedonia: оператор надевает изделие на форму, по окончанию формировки машина сама подбирает изделия в пары, складывает, пришивает этикету, вплоть до упаковки в пакет. Данная линия обслуживается одним оператором. Отдельный человек складывает готовые пакеты с изделиями в транспортные короба, а также снабжает основного оператора артикулами для формировки и расходными материалами для узла упаковки — этикетками, пряжей и другим.
Автоматическая линия формировки Autotex
Подобная организация производства соответствует современным новейшим тенденциям в данной отрасли. Кроме того, она наиболее удобна для интеграции автоматизированной системы контроля.
Не секрет, что приоритетная задача для любого производства — это грамотная организация учета. Если на предприятии нет учета — невозможно им управлять, планировать, повышать эффективность или что-то оптимизировать. На производстве много перемещений сырья, материалов, полуфабрикатов и готовой продукции. На каждом переходе от участка к участку необходима учетная точка, иначе сложно будет управлять фабрикой в целом, а также обеспечить качество и сохранность материальных средств. Каждая учетная точка — это контролеры, над которыми опять же требуется контроль. Контролеру требуются участок (место) и время на приемку и передачу перемещаемой продукции. На практике обычно есть сотрудники, которые руководят работой контролеров. В идеальном варианте службы учета и контроля качества совмещены (это могут быть и разные службы).
Попытаемся минимизировать количество персонала и заменить его программным или техническим обеспечением.
Для решения подобной задачи есть только один способ — создать Автоматизированную Систему Управления предприятием (АСУ).
АСУ — это необходимый инструмент для оценки общей эффективности компании. Какие цели ставит перед собой предприятие при принятии решения о необходимости внедрения АСУ?
Чтобы достичь этих целей, необходимо очень многое сделать на производстве:
Из этих больших стратегических задач можно вывести подзадачи, которые должна решить система автоматизации на производстве, а именно:
Для кого-то, возможно, эти слова покажутся чистой теорией, но в России есть предприятия чулочно-носочной промышленности, на которых АСУ внедрена. Есть предприятия, на которых АСУ внедрена частично или на отдельных участках, наконец, есть фабрики, которые близки к запуску АСУ. Значит, есть и программная, и технологическая возможности такого запуска, и есть специалисты, успешно реализовавшие такие задачи.
На наш взгляд, наибольших успехов на данном поприще добилась компания «Акос Текс» — достаточно молодое и амбициозное предприятие с очень высокотехнологичным производственным корпусом и схемой производственных процессов. «Акос Текс» проектировалась «с нуля» с участием итальянских специалистов как современное предприятие с высоким уровнем автоматизации.
Перед менеджерами компании собственники поставили очень простую, на первый взгляд, задачу — наладить учет и обеспечить понятное и объективное отражение дел на предприятии в любой заданный участок времени. Эта задача потребовала полного переосмысления подхода к организации производства и учета: одновременно с процессом внедрения автоматизированной системы управления необходимо менять технологию производственных процессов, штатную структуру и порядок взаимодействия между подразделениями предприятия.
Такие изменения на производстве под силу только сильной команде из разных специалистов, видящих одну цель. Организацией изменения рабочего цикла занимается команда из 5–10 человек, не считая привлеченных специалистов и специалистов из подрядных организаций. Группа реализаторов проекта состоит из руководителя проекта, проектировщиков по управленческому учету, проектировщиков по регламентированному, налоговому и бухгалтерскому учету, программистов.
Для работы всей системы необходимо корректное внесение первичных данных в любой учетной точке. Для создания такого условия важна подготовка каждого рабочего места: компьютер, канал связи с сервером, программное обеспечение и обученный персонал.
Традиционно программа внедрения АСУ на предприятии совпадает с программой технического перевооружения. Современное оборудование чаще всего проектируется под систему автоматизированного управления или имеет возможность установки такой данной функции. Это накладывает дополнительную нагрузку на персонал — наряду с установкой оборудования необходимо перестраивать технологические процессы, схему документооборота, производственную логистику, сбытовую, финансовую и договорную политику.
Автоматизированный контроль качества изделий
Постараемся раскрыть основные этапы и последовательность внедрения комплексной системы учета на чулочно-носочном производстве.
Как правило, на реализацию такого проекта уходит 1 год. Иногда, по разным причинам процесс может растянуться на 2–3 года. Однако экономическая выгода от внедрения автоматизированной системы учета и контроля значительно превышает затраты на ее создание.
Рассмотрим схему автоматизированного учета производственного процесса вязального цеха:
Все вязальные машины объединены посредством локальной сети с центральным сервером. Современные вязальные машины построены на основе процессоров и функционируют через программное обеспечение. Всем процессом вязания изделия управляет программа, созданная программистом-разработчиком изделий.
В центральном сервере фиксируется текущая информация и информация за предыдущий период. Начальник производства может контролировать режимы работы каждого вязального автомата — время пуска, скорость работы, время простоя по причине обрыва нити или какой-либо неполадки, время заправки нити или устранения неполадки. Очень показательно формирование отчетов по сменам — можно проанализировать выработку одинаковых изделий на одних и тех же машинах и проанализировать эффективность работы каждого сотрудника или смены.
Объединенные отчеты о количестве произведенной продукции поступают в 1 С (или другую учетную программу). Отпадает необходимость в сотрудниках с учетной функцией в цехе. Исключается возможность ошибки подсчета или воровства изделий.
Следующей полезной функцией системы в вязальном цехе является возможность автоматизированного контроля качества изделий и автоматической коррекции программы. В случае выхода параметров изделия за пределы контрольных показателей (например, по причине неоднородности качества пряжи), контрольный прибор автоматически внесет изменения в программу без остановки производства и привлечения дополнительных сотрудников. Кроме того, таким образом, исключается человеческий фактор, при котором разница в параметрах может быть замечена не сразу, а значит, будет отвязано определенное количество брака, который утилизируется или будет продан как второй сорт.
По статистическим данным итальянских компаний внедрение системы АСУ повышает производительность труда на 20%. Между бригадами возникает ситуация соревнования, которая дополнительно мотивируется со стороны администрации путем системы дополнительных поощрений.
Так на практике выглядит учет движения продукции и полуфабрикатов:
Начальник производства (сотрудник, планирующий загрузку производства) распечатывает на каждый вязальный автомат сопроводительный лист с локальным штрих-кодом. Сопроводительный лист вкладывается во внутризаводскую тару и поступает на вязальный автомат. На вязальном автомате идет считывание сканером штрих-кода с сопроводительного листа и автоматическая загрузка программы вязания. По окончанию вязания партии (100 пар) продукция поступает в формировочный цех. При необходимости перемещение может быть зафиксировано сканированием сопроводительного листа с поступлением учетной информации в 1 С.
Этикеточная машина автоматически загружает программу упаковки данного изделия. На принтер поступают данные о том, какую информацию необходимо напечатать на этикетке для данного артикула. Происходит активация/дезактивация тех или иных модулей (например, наклейка стикера и т. д.).
Этикетка сделана универсальной — информация печатается на основании штрих-кода на сопроводительном листе. (В типографии фабрика заказывает универсальную этикетку, информация на которой подходит для всех артикулов. Недостающие и изменяющиеся данные — размер, цвет, состав — наносятся на основании считывания штрих-кода на сопроводительном листе.)
Это дает большой эффект:
Какие рецепты мы можем предложить предприятиям, желающим повысить свою экономическую эффективность?
2014 год для компании Lectra был активным: обновленная версия кожаного раскройного цеха Versalis, новый релиз продукта для создания маркеров и раскладок Diamino, открытие нового офиса компании в Южной Корее, назначение нового генерального директора на европейский регион и Россию г-на Криса Николаеса (с которым наше издание беседовало в сентябре), а теперь - выпуск новой версии программного решения Optiplan, которое направлено на выведение производителей на новый уровень, связь воедино систем планирования, закупок, разработки изделий и производственников.
Читать далее »
В производстве нужно экономить на всем - эта истина была актуальна вчера, актуальна сегодня и будет актуальна завтра. Одна из главных задач для компаний-производителей оборудования - не только предложить клиентам высокотехнологичное и производительное оборудование, но и дать при этом возможность экономить. Итальянская компания MACPI GROUP решает эти проблемы, производя экологически чистое и энергосберегающее оборудование.
Читать далее »
Фирма IMA существует с 1977 года, входит в концерн MACPI GROUP и производит оборудование для раскройного цеха. Более чем 35-летний опыт в производстве вместе с постоянными исследованиями дает современные решения - IMA точно знает, что нужно для идеального кроя.
Читать далее »