Наталья Болдырева: «Расчеты оправдались даже с лихвой»
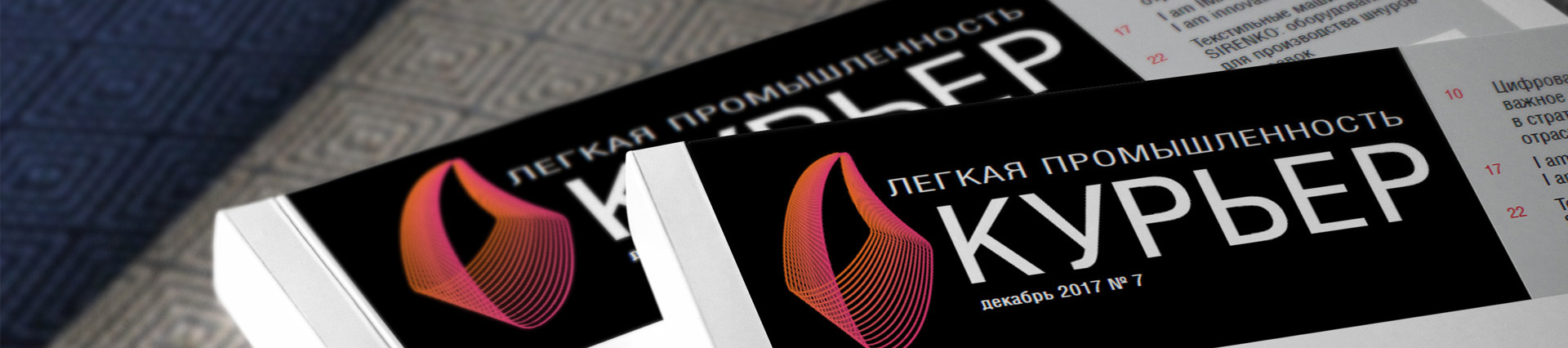
«Спецобъединение» - крупный торгово-производственный холдинг, который выпускает широкий ассортимент спецодежды, спецобуви и средств индивидуальной защиты как собственного производства, так и от ведущих мировых брендов в области охраны труда. С одним из предприятий, входящих в группу, мы познакомимся поближе - это ООО «Спецобъединение Юго-Запад». О самом предприятии и реализации двух проектов - открытии раскройно-подготовительного производства и производства логотипов мы поговорили с директором этих площадок Натальей Болдыревой.
Наталья, давайте сначала расскажем нашим читателям о самом предприятии. Что оно из себя представляет?
Здравствуйте. Сначала хочу поблагодарить за внимание к нашей компании: мы всегда готовы поделиться интересным опытом, тем более, что он у нас имеется.
Фирма основана в 1998 году, в следующем году будет праздновать свой четвертьвековой юбилей. Уже несколько лет подряд входит в пятерку самых крупных и наиболее технологичных производителей спецодежды, обуви и СИЗ.
В мае 2022 года компания открыла сразу две производственные площадки – это раскройно-подготовительное производство и производство логотипов. Обе - на базе складского комплекса, в котором была проведена модернизация помещений.
Группа компаний состоит из четырех основных филиалов - в Москве, Новосибирске, Краснодаре и Барнауле. Наши швейные производства находятся в разных регионах России. Мы практикуем индивидуальный подход к каждому изделию, занимаемся разработкой корпоративного стиля, технологии и общей документации.
Все изделия отшиваются на самом современном оборудовании. В швейных цехах установлены универсальные одноигольные машины фирмы JUKI, двухигольные и краеобметочные, спецмашины, закрепочное оборудование, утюги и парогенераторы ведущих производителей.
Расскажите подробнее о вашей продукции. Это ведь далеко не только спецодежда и СИЗ.
У нас есть практически все, на любой, даже самый взыскательный вкус. Ассортимент очень широк: тут и outdoor, и медицинская одежда, одежда для сферы услуг, для охранных структур, головные уборы и многое другое. При производстве используются материалы и утеплители, проверенные годами, например, Climafort и ШелтерПрофи ST Четыре собственные торговые марки: первая - одежда для работы и жизни I Form, которая отличается высокотехнологичными тканями, удобной конструкцией, эстетическим видом. Вторая линейка – это стильная медицинская одежда Doctor Style. Третья ассортиментная группа - одежда для охоты, рыбалки и активного отдыха Sobol, которая включает в себя полный комплект от нательного белья, арктических курток и брюк до специализированной обуви. Также мы производим трикотажные перчатки «СПЕЦ-SB» и «СПЕЦ-SB» PRO.
В сегменте спецодежды производятся противоэнцефалитные костюмы, термостойкие подшлемники, жилеты сигнальные, брезентовые и спилковые фартуки, антистатические костюмы, костюмы сварщиков, костюмы с защитой от пропила цепной пилы и т. д.
Ваша компания на рынке уже давно. Наверняка среди партнеров есть известные бренды?
Да, действительно, мы сотрудничаем с такими компаниями как Lakeland, UNIVET optical tehnologies, АРМАКОН, РОСОМЗ, РОДНИКИ текстиль, VENTO, GVS Filter tehnology, DELTAPLUS, SAFETY JOGGER, PEZZOL и другие. Безопасность и комфорт своих работников нам доверяют «Норникель», «Новатэк», Черемновский сахарный завод, Сибирская Генерирующая Компания, СГК-Стройгаконсалтинг, Тяжпромарматура, Кубаньэнерго, «Деловые линии», ПИК ГРУППА, СУЭК «Сибирская угольная энергетичекая компания», Мостотрест, Стройтранснефтегаз, Трансмашхолдинг, Мираторг, Газартстрой, РОСНЕФТЬ, «Квадра», Группа «Черкизово», KDV ГРУПП, RENAISSANCE CONSTRUCTION и другие наши любимые партнеры.
А вы сами как давно работаете в компании и за что отвечаете?
Мой личный опыт в швейной промышленности насчитывает уже около 20 лет, три профильных образования. Основные - это инженер-конструктор, технолог и даже бухгалтерия. В компанию меня пригласили в мае 2021 года, в июле доверили проекты по экономическому расчету двух производственных площадок. В данный момент я являюсь директором этих направлений.
Как пришли к идее создания проекта раскройно-подготовительного производства? Какие задачи планировали решить?
В июле 2021 года Анатолий Дегтярев, генеральный директор и собственник нашей компании, поставил задачу открыть две производственные площадки - раскройное производство и производство логотипов. Поскольку объемы компании постоянно растут, ассортимент меняется с учетом потребностей клиентов, появилась идея помочь нашим швейным цехам, подготавливая для них крой. Главная цель заключалась в экономии ткани за счет высоты настилов и концевых остатков, а также экономии времени на раскрой и повышении скорости подачи готового кроя, чего мы и достигли.
Сколько времени понадобилось для воплощения идеи в жизнь?
Примерно месяц ушел на расчет экономической составляющей, сбор необходимой информации и ее обоснования для открытия первой площадки. В сентябре того же года получила от руководства задачу уже по открытию одновременно двух производственных площадок. Далее пошел предпроектный период – это подбор необходимого оборудования, встречи с поставщиками, проекты по строительству, проведению электричества на второй этаж складского комплекса, сжатому воздуху, кондиционированию и вентиляции, подбор штата, обеспечение комфортных условий труда. Мы ведь даже сотрудников набирали и обучали с нуля, подготавливая нужных специалистов «под себя».
В декабре 2021 года был заключен первый контракт и все закрутилось. В январе 2022 года началась стройка.
31 мая состоялось торжественное открытие нашего производства. Точка невозврата пройдена.
Наверное, непросто было рассчитать производительность и другие параметры для такого серьезного проекта.
Как я уже говорила, был представлен достаточно пессимистичный расчет, максимально приближенный к реалиям. Опираясь на свой прошлый опыт, был проведен сравнительный анализ ручного раскроя и с помощью автоматического настилочно-раскройного комплекса (АНРК). Помимо этого, сравнивалось оборудование разных поставщиков, ориентируясь именно на наши потребности, особенности тканей и количество изделий. Параллельно велась работа по прописыванию бизнес-процессов и технологии раскроя. Продумывался каждый шаг, каждое перемещение сотрудников, перенимался опыт коллег, учитывались потребности конечного потребителя,
Ваш опыт может быть бесценен для компаний, которые только планируют приобретением автоматизированного настилочно-раскройного комплекса. Расскажите, с чего вы начали и какие сложности были на пути?
Главное - большое желание и здоровый энтузиазм. Проект получил свой старт со сравнительной таблички в Exсel. Дальше пошло само, тянешь за ниточку и «наматываешь клубочек».
Для того чтобы просчитать экономическое обоснование, нужно собрать максимум информации. Сначала были определены цели и задачи. Цель: открыть рентабельное конкурентоспособное производство кроя, адаптированное под потребности клиентов «Спецобъединения Юго-Запад». Задачи: провести анализ потребности «Спецобъединения Юго-Запад», анализ построения разных раскройных цехов, рынка оборудования, предложения, цен. Необходимо было опираться на стартовый бюджет, просчитать себестоимость, максимально приближенную к реальности.
После - детальная проработка каждого пункта, встречи с поставщиками, рассмотрение коммерческих предложений, подписание контрактов, параллельно планировалась расстановка в помещениях, прописывались технологические процессы, согласования с арендодателем, встречи с такелажниками и прочее. На это ушло примерно три месяца.
Затем начались строительные работы. Были некоторые сложности, но мы справились, всегда находились люди, готовые помочь, подсказать, научить. Потом пошли переговоры, встречи, поиск надежных партнеров, готовых поддерживать наши интересы.
Основная сложность была в том, что параллельно открывались две не зависящие друг от друга производственные площадки, и необходимо было учесть интересы всех участников процесса. Мы попали в сложное время, когда были наложены санкции практически на все, и приходилось быстро искать новых поставщиков и способы доставки. Но наша команда и это преодолела, благодаря мудрости, чуткости и терпению моего непосредственного руководителя, директора по снабжению, Ничикова Вадима.
Какой фактор стал решающим при выборе оборудования?
Основной принцип был - соотношение возможностей оборудования с нашими потребностями, а также немаловажный фактор - постоянная обратная связь с производителем. Наши партнеры в компании IMA полностью закрыли нам эту потребность. Моя коллега увидела их на выставке и передала контакты журнала «Легкая промышленность. Курьер» мне, через вас я уже вышла на официального представителя компании IMA в России Ольгу Непахареву. Через пару дней Ольга приехала к нам в офис, так зародилось наше сотрудничество. Должна сказать, что перед этим мы уже всерьез рассматривали несколько представителей довольно известных компаний, но, как показало время, не благонадежных партнеров. В ноябре из Италии приехали сотрудники IMA на встречу с нами и нашим генеральным директором Анатолием Дегтяревым. А уже в декабре заключили прямой контракт. Чему очень рады.
Какую выбрали модель?
В итоге мы выбрали АНРК - модель последнего поколения серии TYPHOON-70 с высотой настила сжатым воздухом до 7 см. В эту линию входят: машина для настилания и разматывания ткани; машина для настилания полотен и нейтрализатор статического тока; три конвейерных стола, синхронизированных между собой,; машина для резки ткани с автоматической системой покрытия пленкой; устройство смазывания и охлаждения ножа; программное обеспечение для комфортной работы и снятия отчетов в реальном времени. От маркиратора мы отказались, так как в нашем технологическом процессе удобнее использовать готовую бумажную раскладку, но тут каждый подстраивается под свой процесс.
Долго сомневались в выборе между машинами с высотой настила сжатым воздухом 7 см и 3,5 см. Складывали все плюсы и минусы, но остановились на серии TYPHOON-70, все-таки наши сложные ткани подразумевают большую мощность. Хотя для маленьких спецзаказов удобнее будет машина с высотой настила сжатым воздухом 3,5 см. По-хорошему, в производстве нужны обе эти машины. Вторая линия пока в планах.
Были ли сложности с монтажом?
Нам удалось весной 2022 года привезти заказанное оборудование, несмотря на политические сложности в стране, при этом контракт не был просрочен. Одним из условий модернизации складского комплекса было не нарушать целостность здания. Производство запланировано на втором этаже складского комплекса, рассчитывать мы могли только на имеющийся грузовой лифт. По ширине габариты машины не проходили на 20 см, но и здесь было найдено решение: итальянские инженеры создали для нас специальную подставку на колесах по размеру лифта, мы погрузили на нее оборудование под определенным углом и без проблем подняли на второй этаж.
Изначально за нами был закреплен инженер от IMA, полный монтаж оборудования производился под его чутким руководством. Все три секции настилочного стола были собраны и синхронизированы. Настилочная машина и каттер (резак) установлены на рельсы и запущены. Примерно пять дней мы монтировали оборудование. Даже девочки, мастер и операторы, принимали в этом непосредственное участие. Хорошее настроение и позитивный настрой помогали нам.
Тот же инженер проводил полное обучение операторов, непосредственно на месте показывая и рассказывая нюансы, сложности, давая полезные советы. Все очень доступным и понятным языком. В данный момент он находится на связи с нами и постоянно курирует.
Вы сказали, что обучали операторов с нуля. Долго ли пришлось осваивать оборудование? Насколько быстро автоматизированный раскрой встроился в общую технологическую цепочку?
Примерно неделю проходило очень интенсивное обучение. Инженер максимально делился с нами информацией, начиная от механики, заканчивая процессом настила и вырезания. Уже в его присутствии мы начали самостоятельно создавать профили и резать настилы. Конечно, не удалось избежать проб и ошибок, но главное - мы всегда знаем, что есть куда обратиться, и нам помогут.
Сколько человек обслуживает АНРК? Вы работаете в одну смену?
Да, в данный момент в одну, но уже в ближайшее время переходим на две смены На сегодняшний день справляются три оператора, один на настиле, двое на резаке и комплектовке, совместно с ними работают кладовщик и мастер цеха. А пока сместили график операторам: двое работают с 8 до 17, третий с 9 до 18, обед соответственно. За счет этого увеличилось рабочее время реза на два часа.
Как организован процесс, вы довольны производительностью?
В основном мы кроим сложные, воздухонепроницаемые, а также ткани с пропитками и добавлением специализированных нитей. Это такие материалы как Свартекс, Нортси, Наутика, Оксфорд, ветрозащитная, противоэнцефалитные ткани, трикотажные полотна Авертик (антипропил), Гретта, ЛаборЛайт, Премьер Стандарт и т. д.
Сначала заказываем ткань с основного склада, затем раскладчик ее промеряет и делает раскладки лекал в специальной программе AccuMark от наших партнеров компании GERBER, потом загружает их в АНРК, дальше работа цеха. Мастер проверяет раскладки лекал, выстраивает последовательность настилов, делает выпуски продукции с производства, отслеживает сроки и качество. Операторы в свою очередь следят за профилями, качеством и комплектовкой кроя. В смену через комплекс проходит порядка 1000-1200 единиц летней продукции и около 500-700 единиц зимней. Все зависит от заказов, ростовок и видов ткани в одном изделии. Если летняя одежда – это в основном смесовые воздухопроницаемые ткани, можно в один настил постелить до 80-100 полотен (зависит от плотности и толщины ткани), то в зимней все наоборот, количество полотен прямо пропорционально воздухопроницаемости. Приходится создавать новые профили на каждый новый вид ткани. В профили учитывается все: высота настила, скорость и вращение ножа, сила вакуума, плотность полотна, количество полотен и т. д. Все узнавали опытным путем, методом проб и ошибок. Конечно основные параметры нам настроил инженер, но нам все равно постоянно приходится корректировать, подстраиваясь под свои реалии.
Так как оборачиваемость заказов большая, а в сезон сроки маленькие, каждый сотрудник находится на своем и месте и знает свое дело, при этом они все взаимозаменяемы, всегда готовы прийти на помощь друг другу.
А если говорить о сопряженности со швейными производствами, случаются накладки? Как выстроили логистику с регионами?
Компания заранее планирует поставки, поэтому мы работаем по плану. Мы клиентоориентрованы. Конечно, иногда приходится подстраиваться и сокращать сроки, но это уже внутренняя логистика и договоренности со швейными производствами. Все понимают, что в условиях сезона дорога каждая минута.
У нашего предприятия имеются свой автопарк и свои складские комплексы - это более 10 000 кв. м., что обеспечивает неснижаемый запас продукции и своевременную оперативную логистику по всей России. Крой отвозится на фабрику либо «швейники» сами его забирают, это уже работа менеджеров снабжения. Мы, как производство, этого не касаемся, у нас задача выдержать свои сроки. В случае накладок передоговариваемся либо остаемся сверхурочно, чтобы сдать заказ. Но это редко.
Сейчас, оглядываясь на уже пройденный путь, вы можете сказать, что ваши предварительные расчеты оправдались? Есть дальнейшие планы по расширению, модернизации?
Да, конечно, оправдались. Расчеты оправдались даже с лихвой, но мы не останавливаемся на достигнутом. Подобрана очень хорошая команда, переживающая за свое дело, готовая обучаться новому и не останавливаться на достигнутом. Сейчас мы работаем над максимальной автоматизацией рабочих процессов, сокращением человеческого фактора, наладкой внутренних процессов между отделами, прописыванием бизнес-процессов совместно с IT-отделом, бухгалтерией и отделом продаж. Хотелось бы, чтобы каждый сотрудник, приходя на работу, чувствовал свою причастность к большому делу.
Удивительно наблюдать, как все, что ты задумал, просчитал, нафантазировал, реализовалось даже лучше, чем хотелось. Ведь всего год назад это все было только в моей голове, а сейчас мы выдаем полноценные заказы, люди работают в комфортных условиях.
Как уже было сказано, наш ассортимент постоянно меняется и растет, пока, при полной загрузке производства мы закрываем потребности нашей компании в готовом крое только на 15-20 %. Планируем со временем устанавливать дополнительные линии АНРК, расширять штат сотрудников.
Хотелось бы услышать рассказ о вашем втором проекте – производстве логотипов.
Это не менее важный и не менее интересный для нас проект. На нашей производственной площадке реализованы все задумки, установлено оборудование последних модификаций, позволяющее сократить время и при этом обеспечить надлежащее качество продукции. У нас есть цех вышивки, котором работают несколько вышивальных машин фирмы Barudan для изготовления шевронов разной сложности.
А кто помог оснастить вышивальный цех?
Мы уже много лет сотрудничаем со Студией вышивки Дмитрия Адлина. Они поставляют нам оборудование и обслуживают его.
Так же у нас есть печатный цех термотрансферов и цех по нанесению логотипов на готовую одежду и крой И еще мы установили DTF принтер от компании Techno Print, позволяющий в короткие сроки реализовывать полноцветную печать термотрансферов. Аббревиатура расшифровывается как «direct-to-film», то есть «прямо на плёнку». Суть метода в том, что при помощи специального принтера изображение переносится на PET-плёнку, а затем посредством термопрессов этого же поставщика непосредственно на спецодежду.
Экспозиционная камера, промежуточная сушка, двухстоловые пневмопрессы созданы российскими производителями, причем их качество превосходит зарубежные аналоги. Одна из них компания Алексея Самарина Polly Print.
Некоторое сопутствующее оборудование было создано своими руками, что позволило не только сэкономить средства компании, но и обеспечить удобство в использовании.
Сопутствующее оборудование создать совсем непросто. Что именно удалось сделать самим?
Если из крупного, то можно перечислить: сушильные шкафы из влагостойкой фанеры с вентиляцией и терморегулировкой воздуха для изготовления матриц, специальные шкафы с защитным стеклом для удобного использования клеевого порошка, а также стол с горизонтальной подсветкой снизу, что обеспечивает быструю разбраковку термотрансферов в партии.
Также мы используем прямую печать и печать термотрансферов пластизольными красками, что дает снижение себестоимости продукции. В цеху установлена ручная карусель и промежуточная сушка от компании PRINTEX, в планах в скором времени выйти на обороты для автоматического станка.
В нашем коллективе совместно работают дизайнеры и технологи, проводятся тесты и эксперименты.
Спецодежда должна быть не просто удобной и качественной, но и эстетически привлекательной. Для нас не существует мелочей в производстве.
Беседовала Ольга Яковенко
Несмотря на все кризисные явления последнего времени рынок цифровой текстильной печати продолжает развиваться. На сегодня его характерными чертами можно назвать два фактора: практически полное прекращение поставок техники из Европы, США и частично Японии, и предпочтение более доступного оборудования, желательно без потери в качестве печати. Между этими факторами приходится балансировать тем, выбирает оборудование для печати по текстилю для своего предприятия.
Читать далее »
Заканчивающийся 2022 год принес колоссальные изменения как в области международных отношений и внешней торговли, так и в технической и корпоративной политике ведущего мирового поставщика промышленных швейных машин - корпорации JUKI. Прежде всего она вступила в тесные партнерские отношения с компаниями MITSUBISHI и PEGASUS. Фирма «ШВЕЙМАШ» упрочила свой статус официального дистрибьютора корпорации на территории РФ. В статье кратко рассмотрены преимущества сложившегося положения на примере нового оборудования для изготовления спецодежды.
Читать далее »
Европейские бренды видят развитие спецодежды в формате мультиназначения. В этом случае рабочая одежда будет выглядеть, как повседневная или как одежда outdoor - налицо использование функциональных тканей, продуманный дизайн, сочетающий в себе удобство в эксплуатации одежды и её красивый внешний вид, и обязательно проверенное качество всех используемых материалов.
Читать далее »