Юрий Дудченко :Мы стараемся предложить на рынке продукцию быстрее ожидаемого спроса
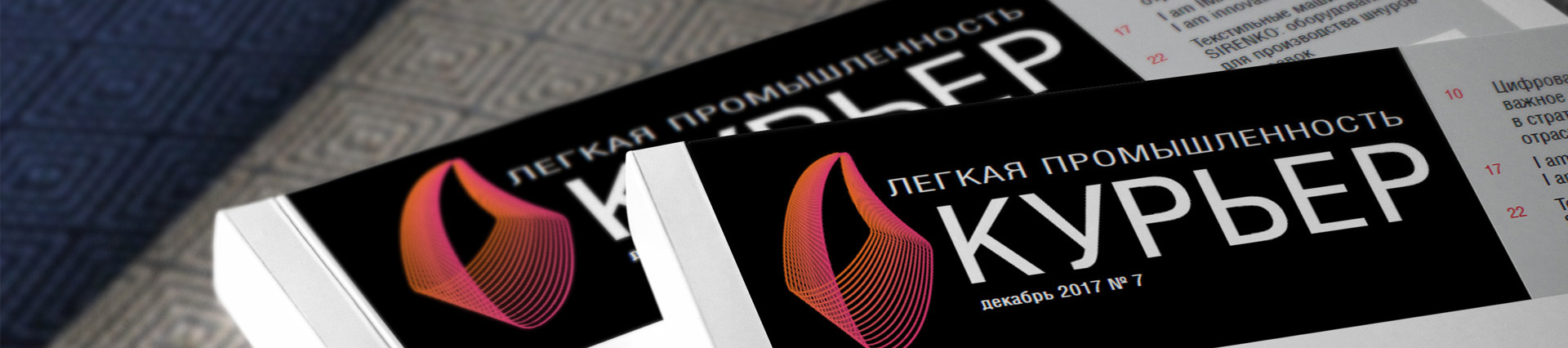
Группа компаний «Энергоконтракт» - российский разработчик и производитель высокотехнологичных СИЗ с мировым именем. Последние два года стали настоящим испытанием для многих предприятий, не исключением стал и «Энергоконтракт», но в качестве антикризисных решений компания наращивала свои мощности, сделав упор на отделочное и швейное производства. О новых проектах и планах мы поговорили с Юрием Дудченко , техническим директором ГК Энергоконтракт .
Юрий Анатольевич, с. какими итогами идет ваша компания в 2023 год? Что удалось осуществить, несмотря на сложившуюся геополитическую ситуацию?
Несмотря на все трудности, которые преподносит текущая реальность, мы постоянно ставим перед собой новые цели и шаг за шагом идем к их достижению.
Мы четко понимаем, что наша продукция необходима людям, которые рискуют жизнью и здоровьем на своих рабочих местах. Мы не можем их подвести, и, чтобы не зависеть от импортных материалов, решили бросить все силы на развитие наших собственных мощностей. За последние два года было завершено два крупных проекта, связанных с расширением отделочного и швейного производств.
Можете рассказать о вашем новом отделочном производстве. Когда был задуман столь масштабный проект и сколько времени потребовалось на его реализацию?
Проект создания второго отделочного производства на сегодняшний день является для нас самым масштабным после строительства ткацко-логистического комплекса, который завершился в 2014 году.
Решение по его строительству было принято в середине 2019-го. Этому способствовало несколько обстоятельств: рост объема выпуска готовой продукции и задача по увеличению доли производства ткани на собственных площадках. Двукратно увеличив количество технологического оборудования для обработки ткани, мы получили возможность более гибко реагировать на запросы клиентов по ассортименту цветовой гаммы и времени выполнения заказа. Для реализации данного проекта было приобретено здание общей площадью 4,5 тыс. м2, в котором мы провели реконструкцию, превратив его из супермаркета в помещение производственного назначения. В нём разместились цех обработки ткани с новейшим комплексом оборудования очистки стоков, склад ткани и участок разбраковки материалов. Кроме того, в здание была встроена газовая котельная мощностью 4,5 МВт для производства пара для технологических целей. Параллельно была осуществлена его газификация, а также организованы подъездные пути и погрузочно-разгрузочные точки.
Описание основного перечня работ занимает всего несколько строчек, но на самом деле на все это потребовалось два года упорного труда целой группы наших специалистов. Старт реконструкции здания выпал на начало пандемии, срок в срок, день в день. Мир замер. Нам тоже пришлось притаиться на пару-тройку месяцев.
Затем на всех надели маски, и работа закипела. Ждать было нельзя. Ведь далеко в Италии и Германии уже приступили к изготовлению технологического оборудования для отделочного производства, заказанного в самом конце 2019 года.
Для создания отделочного производства вы выбрали оборудование европейских производителей. Расскажите подробнее о нем и технологиях.
Выбор производителей, разумеется, далеко не случаен. Чтобы получить качественный продукт, необходимо использовать оборудование, которое сможет воспроизвести и поддерживать все заданные параметры. Оно должно быть долговечным, ремонтопригодным, иметь достаточный технологический потенциал для использования его в перспективе. Этим критериям соответствует европейское оборудование известных немецких и итальянских марок.
Выбор пал на проверенный годами высокотемпературный красильный аппарат джиггер немецкой компании THIES и сушильно-ширильную машину итальянской UNITECH. Эти бренды присутствуют на нашем производстве с 2011 года. Изменять традициям не стали. Опыт эксплуатации дал нам возможность усовершенствовать конструкцию новых единиц. Наши партнеры в Германии с немецкой педантичностью интегрировали все технические обновления в джиггер, о которых мы просили.
Фактически мы совместно с производителями вывели их продукт на новый уровень. Значительные изменения были внесены в систему нагрева и циркуляции раствора, трансформирована конструкция приготовительных баков и, наконец, сам восьмитонный аппарат стал поставляться на монтажной платформе, что сократило время на его установку до одного действия – «просто поставить». Последнее нововведение мы предложили, поскольку просто не имели возможности делать дорогостоящий фундамент под эту машину, да и еще на втором этаже здания, где размещается наше второе отделочное производство. Видимо, и сам поставщик считает это решение эффективным, так как теперь оно красуется на всех рекламных буклетах компании THIES.
Сушильно-ширильная машина также претерпела значительные технические модификации по сравнению с установленной на первом отделочном производстве. Прежде всего она стала длиннее на 15 метров и получила газовый нагрев. Это позволило сократить себестоимость обработки ткани. Благодаря газовому нагреву и увеличению количества сушильных камер мы снизили производственные затраты и достигли еще более высокого качества продукции. Также получили ряд преимуществ, применив две последовательно установленные камеры для пропиток. Комплекс всех технических нововведений позволил сократить время пропитки ткани почти в два раза. Соответственно, мы получили возможность увеличить объем производства.
А в чем состоит уникальность ваших технологий отделки?
Причина уникальности – в самих тканях. Крашение и обработка арамидных тканей – это сложная технология. И если набор технических средств понятен и доступен к использованию, то подбор техпроцесса и рецептур применения химических элементов – нетривиальная задача. Она требует не просто высокой квалификации от сотрудников, но и творческого подхода в поиске и отработке того уникального, единственно верного решения, которое в итоге и позволяет добиваться высоких результатов в отделке и крашении арамидных тканей. На сегодняшний день наработано более 100 оригинальных рецептур, которые позволяют обеспечивать любые потребности наших заказчиков, а также предлагать им более уникальные продукты. Всё это наше ноу-хау.
Ассортимент продукции увеличился?
Что касается увеличения - к этому мы готовы. Наши специалисты из профильных отделов постоянно работают над разработкой новинок. Мы можем судить об этом по количеству всевозможных экспериментов, которые проводятся совместно с нашим производством и лабораторией.
Создать столь высокотехнологичное производство сложно, а в условиях санкций - крайне сложно. Как вам это удалось? Что пришлось преодолеть?
Основную часть этих двух проектов мы успели закончить еще до санкций, а после их введения максимально ускорились. Ближе всего мы столкнемся с негативными последствиями в процессе планируемой поставки промывной линии, но надеемся, что многолетнее сотрудничество с производителями оборудования, а также нашим давним партнером ООО «Маштексимпэкс» помогут преодолеть все трудности.
Кроме того, санкции оказывают влияние на оперативность поставок запасных частей и комплектующих. Нарушены ранее выстроенные логистические цепочки. Сейчас мы уже отработали новые, но время поставки увеличилось. В связи с этим мы пересмотрели сроки планирования закупок.
Без высококвалифицированного персонала в реализации подобных проектов не обойтись. Компании-производители оказывали помощь, или вы справились собственными силами? И как обстоят дела с кадрами?
Для выполнения монтажных и пусконаладочных работ нам была необходима помощь специалистов производителей, которые всегда приезжают к заказчикам оборудования и выполняют самые ответственные операции самостоятельно. Срок приезда монтажников запуска на сушильно-ширильной машине и джиггере совпал с периодом максимально жёстких ограничений на въезд в Россию. Для того, чтобы подать документы на оформление приглашения на визу, нам пришлось получать дополнительное разрешение в Министерстве промышленности и торговли РФ. Это усложнило нашу работу и увеличило срок подготовки документов на въезд, однако мы с честью вышли из этой непростой ситуации и смогли организовать все монтажные и пусконаладочные работы в срок.
Одновременно решались сложные задачи по подготовке кадров. Мы заблаговременно приняли в штат новых механиков, которые обучались работе с оборудованием отделочного производства непосредственно в ходе его сборки. Практика показала высокую эффективность такого подхода: когда настал момент запуска, они уже имели необходимую подготовку и с первых дней приступили к выполнению своих обязанностей в штатном режиме.
Количество сотрудников отделочного производства с открытием нового цеха увеличилось на 39 человек, из них 2 инженерно-технических работника. Подбор персонала на должность операторов оборудования осуществлялся из числа ранее принятых транспортировщиков-упаковщиков, что способствовало их карьерному росту. Обучение проводили мастера смены и операторы, которые имеют большой опыт работы на оборудовании российского производства. Это наша проверенная практика – готовить специалистов самостоятельно, так как рынок труда не может удовлетворить наши потребности, узкопрофильных специалистов никто не готовит.
Есть ли аналогичное вашему отделочное производство в России, Европе, или вы действительно уникальный производитель?
Я часто сталкиваюсь с подобным вопросом и всегда однозначно отвечаю, что все производства в своем роде уникальны. И связано это со многими факторами, такими как цели и задачи, которые стоят перед производством, специфика работы с материалами и их особыми свойствами, конфигурация помещения, особенности инженерных систем и коммуникаций, внутренней и внешней логистики и многим другим. Хороший пример – кухня в ресторане. Набор оборудования, посуды, плиты и духовки – примерно одинаковый, исходные продукты – схожи, а вот блюда на выходе очень различаются. Все зависит от «шефа» и коллектива. В этом и есть уникальность. Самое главное, чтобы изделие на выходе соответствовало всем предъявляемым к нему требованиям. А еще лучше, если в производстве уже изначально заложен потенциал на перспективное увеличение объемов, ассортимента и роста качества продукции. Тогда можно с уверенностью сказать, что средства израсходованы не зря и мы сделали свою работу хорошо.
И можно ли сказать, что вы сработали на импортоопережение?
По поводу импортоопережения – вопрос сложный. Отчасти – да, это так. Мы стараемся предложить на рынке продукцию быстрее ожидаемого спроса на нее и ведем работу в этом направлении. Это один из способов оставаться лидером в сегменте. Но, по большому счету, чтобы работать на импортоопережение, нужно создавать и строить свое оборудование, технологии, производить свое сырье и сопутствующие материалы. Готовить специалистов во многих областях. А это уже задачи государственного масштаба.
Для создания конечного продукта вы модернизировали и швейное производство. Мы писали в № 3/2021 года о вашем приобретении АНРК ATRIA. А что вы смогли усовершенствовать в этом году?
Для увеличения мощности швейного производства нам пришлось произвести перепланировку нескольких этажей производственного здания с модернизацией инженерных коммуникаций. В ходе реконструкции прошло масштабное «переселение» ряда подразделений со всем технологическим оборудованием. Это было непросто, но позволило нам повысить эффективность логистики внутренних перемещений полуфабрикатов между ними. Реконструкцией было затронуто более 3,5 тыс. м2, а на площади более 1,6 тыс. м2 провели косметический ремонт.
Параллельно велась закупка оборудования для организации новых швейных бригад. В общей сложности приобретено 179 единиц современного швейного оборудования от ведущих мировых производителей, а также более 800 вспомогательных устройств, средств механизации и прочих необходимых в цеху предметов. Благодаря этому расширению мы в два раза увеличили количество швей, организовав новые рабочие места.
. Для производства изделия необходимо выполнить большое количество разнообразных операций, каждая из которых имеет свои особенности и специфику, и потому требует соответствующую машину. Результат этих операций напрямую зависит от возможностей и качества аппаратов. Продукция японских производителей JUKI и Kansai применяется как основное оборудование. Практически постоянно мы прорабатываем вопросы по увеличению производительности и сокращению потерь в наших производствах. Ведем работу по замене решений на более технологичные. К большому сожалению, многие компании ушли с российского рынка, и даже параллельный импорт не всегда позволяет компенсировать эти потери.
Группа компаний «Энергоконтракт» всегда была и является первой в вопросах охраны и безопасности труда, в создании средств СИЗ. Вы первые создали костюм с защитой от электродуги, комбинезон с защитой от пара и горячей воды, боевую одежду пожарного. Что еще появилось в вашем арсенале впервые и какие новинки планируете показать на выставке БИОТ?
На выставке будет представлена новая дугостойкая коллекция, которая полностью перевернет восприятие специальной защитной одежды. При ее создании мы ориентировались, во-первых, на повышение комфорта СИЗ, стремясь к уровню, сравнимому с outdoor-одеждой, во-вторых - на разработку дизайна и форм, приближенных к повседневному стилю. Также мы презентуем комплект «Металлург» из арамидной ткани с алюминизированным покрытием и демисезонный огнестойкий костюм повышенной видимости, который, в первую очередь, предназначен для нефтегазового сектора. Он сделает работу сотрудников в осенне-весенний период, когда в летнем комплекте холодно, а в зимнем – еще слишком жарко, комфортнее. Кроме того, среди новинок можно будет увидеть универсальную привязь 4 в 1 для проведения работ на высоте, она станет альтернативой продуктам премиум-сегмента иностранных производителей, ушедших с рынка.
Немного о ваших дальнейших планах на 2023 год. Какие производственные участки планируется модернизировать?
В данный момент мы работаем над проектом преобразования цеха текстильной печати, что даст нам возможность использовать еще более эффективные технологии для нанесения логотипов и светоотражающих элементов на СИЗ. Вопрос о его расширении и модернизации назрел пару лет назад, но мы не могли приступить к его реализации, так как все ресурсы были сконцентрированы на обновлении швейного подразделения и строительстве второго отделочного производства. Сейчас мы активно готовимся к старту проекта, разрабатываем план и график мероприятий. В самое ближайшее время приступим к его исполнению. На самом участке также уже ведутся некоторые подготовительные работы.
В активной фазе приобретение новой уникальной линии для промывки ткани. Все необходимые предварительные усилия уже предприняты, с производителями обсудили все технические аспекты и утвердили технологическую конфигурацию. Готовим контракт и обсуждаем варианты поставки.
В скором будущем изменения ждут также стегальный цех - замена одной из машин, которая физически и морально устарела. А в начале 2023 года рассчитываем завершить обновление участка очистки воды, дооснастив его оборудованием для охлаждения горячих стоков. Это позволит сократить расходы на эксплуатацию высокотехнологичной системы.
Беседовала Ольга Яковенко
Одним из трендов последних лет в индустрии моды является использование металлизированных эффектов. Декорирование фольгой KURZ для текстиля и кожи в настоящий момент - это один из самых популярных и эффективных способов отделки. Возможности фольги чрезвычайно широки и активно используются производителями ткани, одежды, обуви и аксессуаров.
Читать далее »
Казалось бы, патроны, катушки, бегунки, трубки – такие незначительные детали в производстве текстильной продукции, но на самом деле именно данные элементы в многогранной цепочке изготовления текстильных изделий играют немаловажную роль.
Читать далее »
«БТК групп»– крупнейший вертикально интегрированный холдинг легкой промышленности России, предприятие полного цикла. На данный момент деятельность холдинга охватывает такие сферы как разработка и производство инновационных тканей, полотен, материалов, одежды самого разного назначения.
О том, как чувствует себя такой флагман в океане непростых нынешних экономических условий, как развивается и куда держит путь, мы поговорили с руководителями ключевых направлений компании.
Читать далее »